Written By: Moiz Majid
Improvement in bio-plastics
In the near future, it
is evident that petroleum will run out. This will increases the prices of
petroleum products. Although about 4 to 5 percent of the total oil is being
used in the production of plastic resins, but the whole world is crying for the
disposal of plastic waste. Each year 348 million tons of plastic is produced,
half of which is added as waste in the environments mostly in the seas and
rivers where it is the major cause of marine deaths. Globally, manufactures
produce 348 million tons of plastic each year, compared to 1.5 million tons in
1950. Normally plastic items take 1000 years to degraded totally to landfills,
but the plastic bags we use in our daily life take 40 to 50 years to degrade
completely while plastic bottles take 450 years. This concern is in part
translated in the form of market demand for eco-friendly products made of
renewable raw materials. This issue stimulated the demand for harmless and
biodegradable materials. From there evolve the idea of recycling. The focus
shifted to the production of plastic from renewable sources. Bio polymers are
special polymers that involve living organisms in its synthesis process, it can
be partially or totally produced from natural renewable materials. They can be
extracted directly form biomass, bu micro organisms or with the precipitation
of bio intermediaries. They can be molded by heat or pressure actions because
they contains bio polymers in different percentages. Plastics that are bio
based are replacing plastic made of petroleum due to it has the same properties
as synthetic plastic. The use of synthetic mastic takes a long time to
decompose in nature as discussed earlier. If synthetic plastics are burnt down
it releases harmful gases into atmosphere such as carbon dioxide, sulfur dioxide,
methane and carbon monoxide etc. On the other hand, bio based plastics or
starch based plastics do not exist harmful gases. Plants such as maize, banana,
cassava, potatoes, rice etc are rich in starch. Starch is the major
carbohydrate in plant that contains amylopectin and amylose molecules which can
improve mechanical properties. The content of starches derived from cassava
plants may be used as bioplastics due to plenty of availability, high starch
content in cassava plant. The addition of concentration of cassava starch can
increase hardness form 31.56 to 67.99shore A, increase density of 1.164 to
1.191 gram per centimeter cube and accelerate the decomposition process (complete
decomposition occurs on the 12th day) is affected by oxygen content in carbohydrates
the amount of cassava starch and moisture absorption. Starch based
bioplastic nanocomposites represent an exciting and promising alternative
to conventional plastics owing to their markedly improved performance
in mechanical, thermal, barrier as well as other physical and chemical
properties. Many companies and research institutions have taken a
strong interest and invested heavily in the development of starch based
bioplastic nanocomposites. Polymer nanocomposites are generally known
to offer better performance with significant weight reduction and
affordable materials for transport industries such as automotive and
aerospace. The first commercial product of a polymer nanocomposite is
the timing belt cover which was made from nylon 6
nanocomposites
by the Toyota Company. The timing belt demonstrated good rigidity and
excellent thermal stability. The timing belt was shown to save up to
25% weight due to the lower content of nanoclays used. In addition,
nylon 6 nanocomposites have been used to fabricate engine covers, oil
reservoir tank and fuel hoses in the automotive industry due to
their remarkable increase in heat distortion temperature (HDT) as
well as their enhanced barrier properties and mechanical properties.
Thermoplastic olefin nanocomposite reinforced with as little as 2.5%
clay particles has also been employed by General Motors. In recent
years, there has been increased use of biopolymer nanocomposites by
various vehicle manufacturers to make both external and internal
parts such as mirror housings, door handles etc. The weight
advantage
of polymer nanocomposites has a significant impact on environmental
protection.
Bioplastics
made from starch reinforced with clay particles have outstanding barrier
properties that would result in considerable enhancement of shell life
for many packaged foodstuffs. These nanocomposites demonstrate
optical transparency in addition to biodegradability which is impossible to
achieve with conventional synthetic polymer composites. Starch based
packaging plastics are odorless, non-toxic and display low permeability to
oxygen especially at low relative humidity. These property
advantages make the new generation of nanocomposite bioplastics
widely
acceptable in packaging industries as wrapping films and beverage
containers. Bayer research group played a significant role in developing a
new grade of plastic films for food packaging made from nylon 6 nanocomposites.
InnoWare Atlanta, USA, recently successfully developed starch based food
packaging containers with the ability to withstand high temperature,
which is especially important during transport and storage. Therefore,
starch based packaging materials have great potential in providing proper
packaging materials for safe, wholesome food
products
which has been the focus of food packaging industry for many
years. The classical drug administration by injection causes the
plasma levels to go up and fall drastically when the drug has been
metabolized; leading to a cyclical pattern each time a dose is
administered. Therefore, in classical drug administration, most of the
drug plasma levels can be outside the optimal range. Due to this, the
drug permeates throughout the body and is not targeted to the site
where it is specifically required. To overcome this problem, a controlled
drug delivery mechanism in
which
the drug is released at a constant, preset rate, preferably close to the
specific location is required. One of the notable approaches is to contain
the drug in a polymer membrane, from which it diffuses out into the
tissue in which the membrane is implanted. Duncan and Kapecek [18]
reported that various polymers to which certain drugs were attached could
be used to release the drugs after cleavage of the bonds attaching them to the backbone. Recently, attempts to
use starch based biodegradable plastics have indicated enhanced drug
delivery and eliminated the need for surgical retrieval of the polymeric
material after drug administration. The differential rates of drug
release demonstrated by this method of drug delivery may
be beneficial in cases where increased drug dosage is necessary at
the beginning of therapy. It is observed that clay nanoparticles are
cost effective and versatile raw materials for starch
based nanocomposites due to their unique layered structure, abundance
in nature and wide availability. When clay based nanoparticles are applied
to fabricate starch based bioplastics, enhanced properties
are demonstrated. Moreover, the very low level of clay in the matrix
makes the overall density similar to that of pure polymer. Clay based
nanocomposites have found wide use in production of
environment-friendly automotive parts and packaging materials. Their
future markets will further expand from the current automotive and
packaging industries to other industries
such as electro
materials, sensors and biomedicine. Other potential applications for
starch-based
nanocomposites for
bioplastic materials are also currently being investigated. However,
in spite of the successes achieved in the development of clay-based
nanocomposites, their design, manufacturing and applications are
often empirical and their large scale applications are still at
their infancy stages.
The reasons may be due to the limited theoretical knowledge on the
novel
nanostructure
materials and the modification of clays for the purpose of targeted
bioplastic, the mechanisms for superior reinforcement as compared to
their micro-counterparts and the establishments of a
simple processing structure-property relationship.
Further developments of starch based bioplastic nanocomposites will
depend largely on the
understanding of the
above fundamental concepts. Most nanocomposite fabrication methods
have reported nanoparticle agglomeration causing formation of
irregularly shaped Nano structural features within the composite. Noting
that enhancement of properties of nano biocomposites is achieved when clay
particles are well dispersed in the polymer matrix,
improved properties of these materials can only be attainable
if nanoparticle inclusions are of uniform size and shape and of very
good degree of dispersion. Future research is therefore expected to
address the following issues and challenges:
1.develop a simple
but effective way to modify clay minerals and improve their
compatibility with desirable polymer matrix since dispersion of clay
platelets directly affects the final structure and hence the final
properties of bioplastic nanocomposites, design an effective
experimental technique to effectively fabricate nanocomposite.
2.bioplastics with
uniformly dispersed nanoparticles and to establish optimal
processing-structure-property relations to facilitate the design of
nanocomposite
3.bioplastics for
specific applications. It is also proposed that future works should use
carbon nanotubes in the fabrication of nanocomposite bioplastics.
References:
L. Janssen, L.
Moscicki, Thermoplastic Starch, Willey-VCH Verlag GmbH & Co. KGaA, 2009.
Q.X. Zhang,
Z.Z. Yu, X.L. Xie, Kimiyoshi naito and yutaka kagawa, preparation and
crystalline morphology of biodegradable starch/clay nanocomposites, Polymer 48
(2007) 7193-7200.
M.F. Huangu,
J.G. Yu, X.F. Ma, Studies on the properties of montmorillonite-reinforced
themoplastic starch composites, Polymers 45 (2004) 7017-7073.
D. Carvalho, A.J.F. Curvelo, A.A.S. Agnelli, A First
insight on composites of thermoplastic starch and kaolin, Carbohydrate Polymers
45 (2001) 189-194.
V.P. Cyras,
L.B. Manfredi, M.T. Ton-That, A. Vazquez, Physical and mechanical properties of
thermoplastic starch/montmorillonite nanocomposite films, Carbohydrate Polymers
73 (2008) 55-63.
Suksankraisorn K., S. Patumsawa, Vallikul P.,
Fungtammasan B., and Accary A., “Cocombustion of municipal solid waste and thai
lignite in a fluidized bed,” Energy Convers. Manag., vol. 45, no. 6, pp.
947–962, 2004.
Avella
Maurizio, De Vlieger Jan J., Errico Maria Emanuela, Fischer Sabine, Vacca
Paolo, and Volpe Maria Grazia, “Biodegradable starch/clay nanocomposite films
for food packaging applications,” Food Chem., vol. 93, no. 3, pp. 467–474,
2005.
Gáspár M., Benko Zs, Dogossy G., Réczey K., and
Czigány T., “Reducing water absorption in compostable starch-based plastics,”
Polym. Degrad. Stab., vol. 90, no. 3, pp. 563–569, 2005.
Alves Vanessa
Dias, Mali Suzana, Beléia Adelaide, and Grossmann Maria Victória E, “Effect of
glycerol and amylose enrichment on cassava starch film properties,” Food Eng.,
vol. 78, no. 3, pp. 941–946, 2007.
Wahyuningtiyas Nanang Eko, Suryanto Heru, Rudiyanto
Eddy, Sukarni, and Puspitasari Poppy, “Thermogravimetric and kinetic analysis
of cassava starch based bioplastic,” J. Mech. Eng. Sci. Technol., vol. 1, no.
2, pp. 1–16, 2017.
Oladunmoye
Olufunmilola O, Aworh Ogugua C, Maziya-Dixon Bussie, Erukainure Ochuko L, and
Elemo Gloria N, “Chemical and functional properties of cassava starch, durum
wheat semolina flour, and their blends,” Food Sci. Nutr., vol. 2, no. 2, pp.
132–8, 2014.
Myllarine Paivi, Partanen Riitta, Seppälä Jukka, and
Forssell Pirkko, “Effect of glycerol on behaviour of amylose and amylopectin
films,” Carbohydr. Polym., vol. 50, no. 4, pp. 355–361, 2002.
Lopez Oliva V.,
Castilo Luciana A., Garcia M. Alejandra, Villar Marcelo A., and E. Silvia,
“Food packaging bags based on thermoplastic corn starch reinforced with talc
nanoparticles,” Food Hydrocoll., vol. 43, pp. 18–24, 2015.
Ashby Michael
F., Materials Selection in Mechanical Design, Third Edit. 2005.
Bastioli
Castia, Handbook of Biodegradable Polymers, vol. 128, no. 4. Rapra Technology
Limited, 2005.
Sharma, C., Manepalli, P.H., Thatte, A., Thomas, S.,
Kalarikkal, N. and Alavi, S. (2017) Biodegradable Starch/PVOH/Laponite RD-Based
Bionanocomposite Films Coated with Graphene Oxide: Preparation and Performance
Characterization for Food Packaging Applications. Colloid and Polymer Science,
295, 1695-1708.
Averous, L.,
Fringant, C. and Moro, L. (2001) Starch-Based Biodegradable Materials Suitable
for Thermodynamics Packaging. Starch/Starke , 53, 368-371.
R. V. Gadhave et al. DOI: 10.4236/ojpchem.2018.82003
29 Open Journal of Polymer Chemistry
Carraher,
C.E.Jr. and Sperling, L.H. (eds.) (1983) Polymer Applications of
Renewable-Resource Materials. Plenum Press, New York.
Ching, C.,
Kaplan, D. and Thomas, E. (eds.) (1993) Biodegradable Polymers and Packaging.
Technomic Publishing Company, Inc., Lancaster.
Tharanathan,
R.N. (2003) Biodegradable Films and Composite Coatings: Past, Present, and
Future. Trends in Food Science and Technology , 14, 71-78.
Zubris, K.A.V.
and Richards, B.K. (2005) Synthetic Fibers as an Indicator of Land Application
of Sludge. Environme ntal Pollution, 138, 201-211.
Brinton, W.F.
(2005) Characterization of Man-Made Foreign Matter and Its Presence in Multiple
Size Fractions from Mixed Waste Composting. Compost Science & Utilization,
13, 274-280.
[8] Thompson,
R., Moore, C., Andrady, A., Gregory, M., Takada, H. and Weisberg, S. (2005) New
Directions in Plastic Debris. Science, 310, 1117.
Advertisement
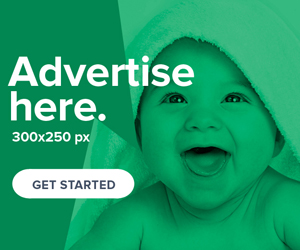
EmoticonEmoticon